This is a guest post by Derrick Martin. If you have a similar problem with your Hammerli, feel free to contact Derrick at ask_derrick@aol.com.
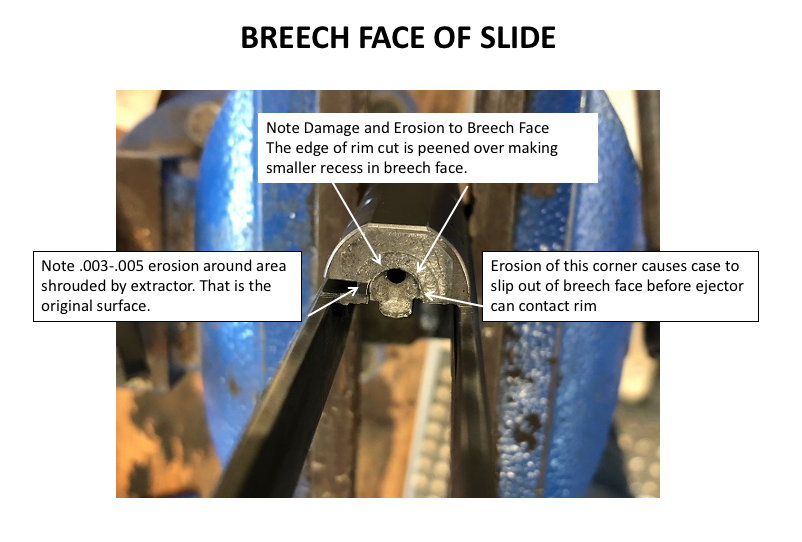
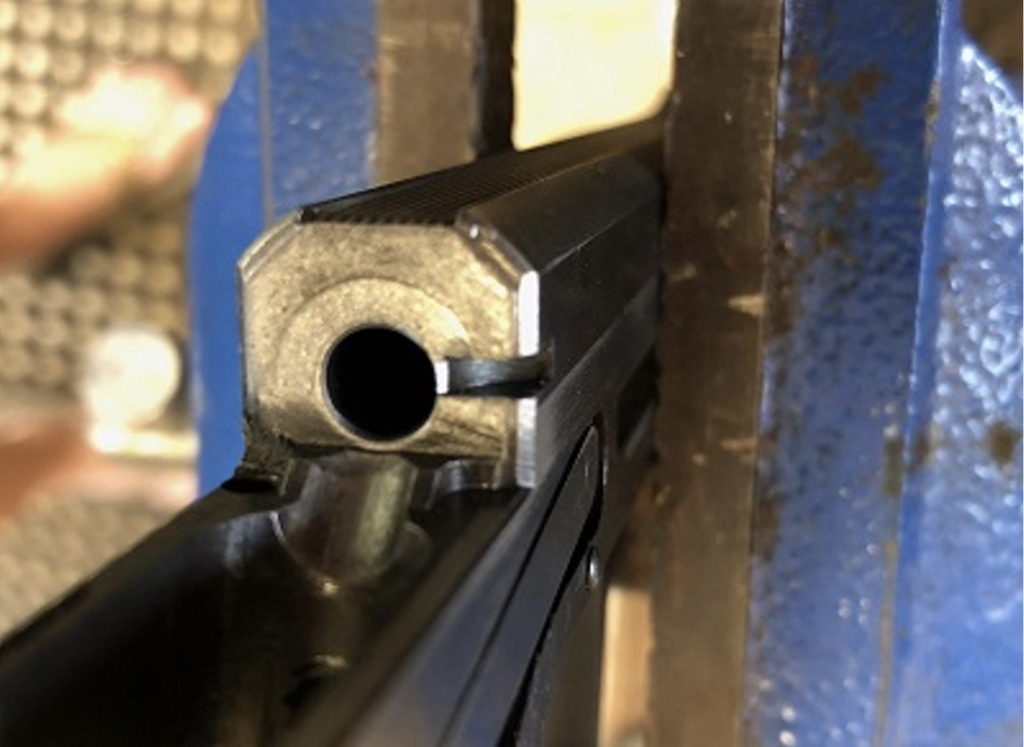
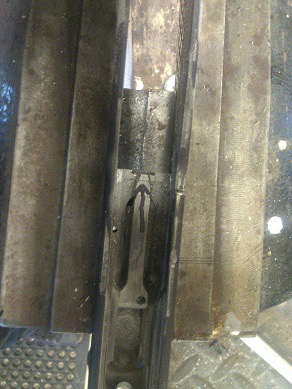
BREECH FACE CUTTER
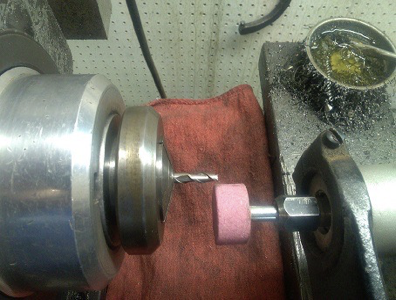
The Counterbore had a large radius around the Pilot Hole. I had to reface counterbore back to remove radius and then regrind cutting reliefs with die grinder, back into counterbore teeth. Cutter reliefs were also ground into pilot teeth to ensure counterbore in breech face was carried thru to pilot hole.
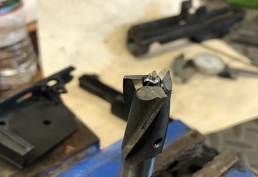
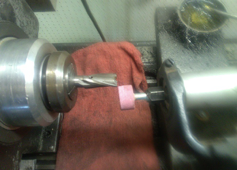
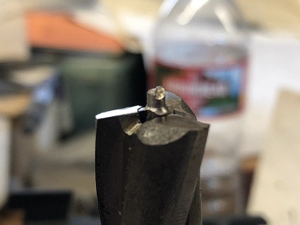
SLIDE SETUP IN MILL
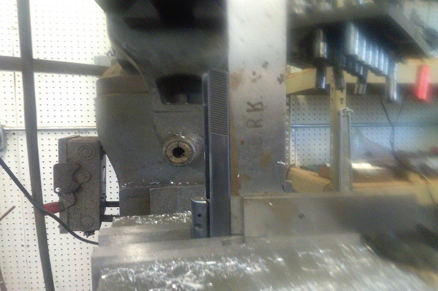
The rim of a 22LR case is .043” thick, we need to make an insert that has the .043 cut and enough material to support the case. I decided to make the insert .103 thick, and the counterbore .100 deep to allow for the .003 erosion of breech face and barrel face. I doubt it is critical, but it seemed to be right.
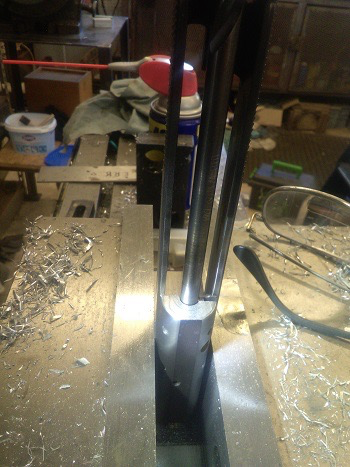
Lets verify some math, so you see what I did. Drill is .250, running out .005 for inscribed circle of .260. Rim cut in slide is around .275, so I could move table about .0075 to contact on each side. I could then contact at top of rim cut and come back .0075 to be centered in breech face. This was when I discovered the center of the breech face was about .005 from the measured center of the slide. I measured slide at the top, so it could be warped/bent or not completely true in vise. Either way, I was now truly centered in the breech face.
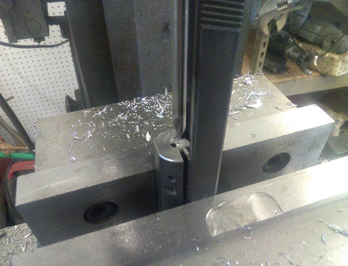
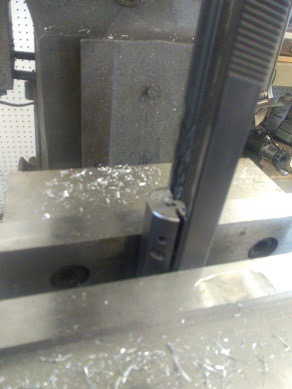
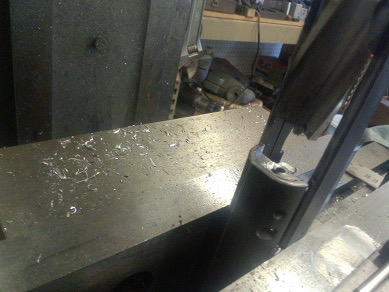
Use back gear and go slow, removing chips and oiling frequently. Make counterbore .100 deep.
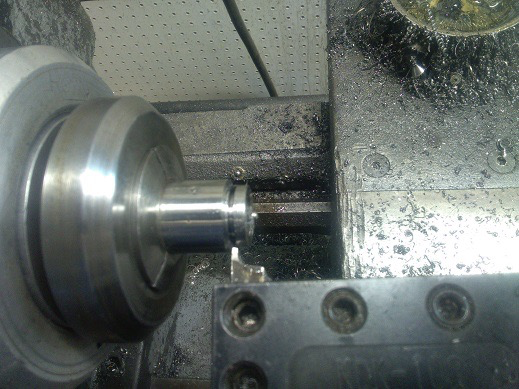
I used a piece of 416 Stainless, because I had it. Actual material isn’t too important, as long as it isn’t dead soft and it can be silver soldered.
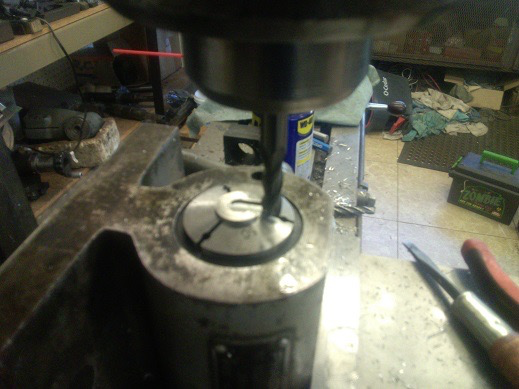
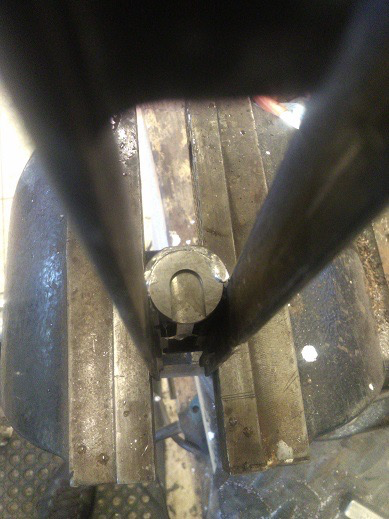
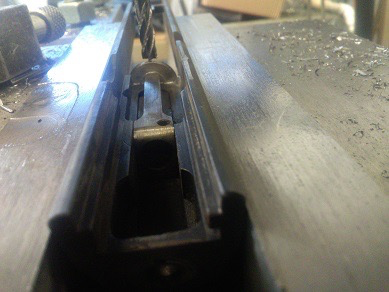
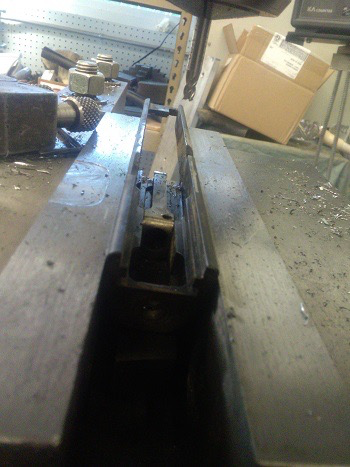
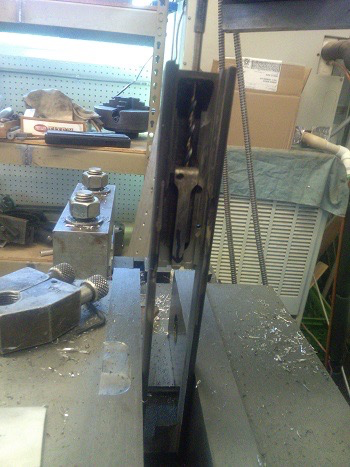
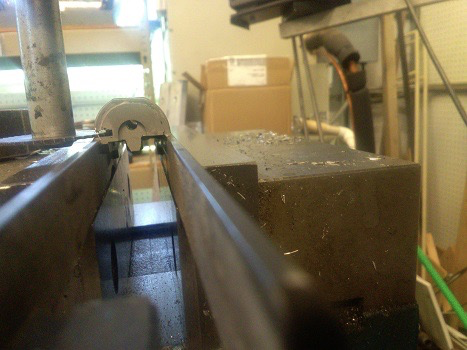
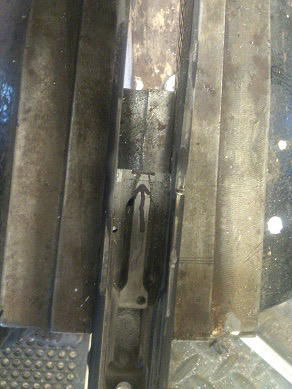
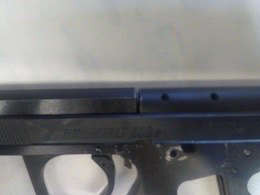
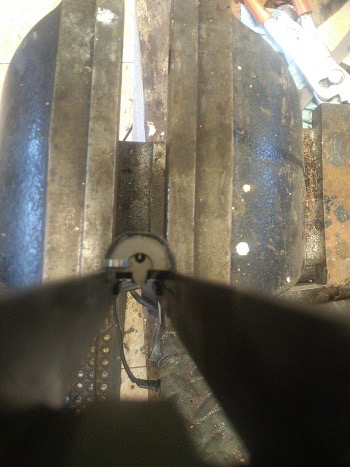
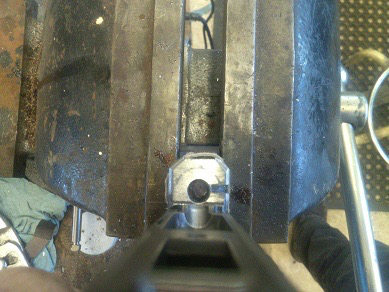
Derrick Martin is the former owner of Accuracy Speaks Gunsmithing in Mesa, AZ. He has 40 years experience in Competitive Shooting and Gunsmithing. He is retired now, but remains available in the shop for interesting projects. His email address is ask_derrick@aol.com